Miyoshi Inc.-The maker’s choice is an environmentalist
Produce things not to be wasted
“We aim to reduce wastage in our society by producing things not to be wasted.” This is a firm determination of Koji Sugiyama, the CEO of Miyoshi Inc., a factory manufacturing simple molds for injection molding.
This is rather an odd comment from a factory owner, which its existence relies on consumption of the products by the consumers. Wastage is embedded in its business.
But for a former engineer in environmental science, observing enormous wastage day after day at waste disposal plants as a site manager, the endless act of wasting products and our natural resources is something intolerable.
So when he decided to succeed his family business, he determined to do something in his own way to reduce wastage and preserve our environment.
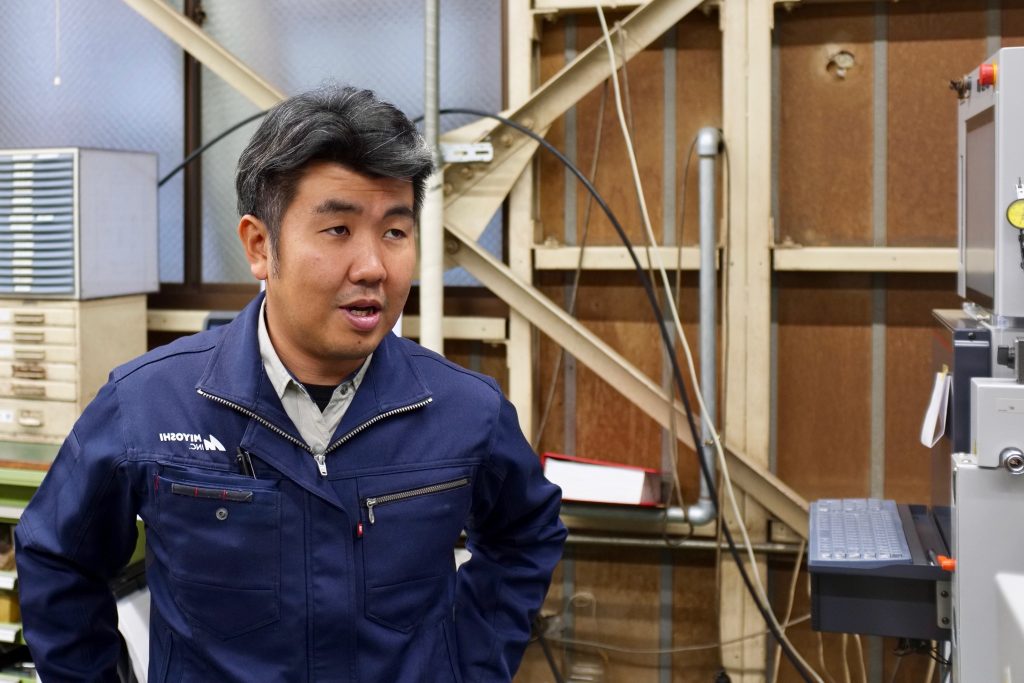
Miyoshi Inc. - The maker's choice
As a typical small factory in Tokyo, Miyoshi is mingled and hidden in a housing area in the city of Katsushika: a 20-minute walk from Shin-Koiwa Station. It’s hard to notice from outside if you are a stranger.
But the company is well known by the top product designers in Japan as the maker’s choice for a manufacturer of a simple metal mold for an injection molding.
Founded in 1972, it specializes in prototyping and small volume production for precision plastic products, using skills and technologies harnessed by decades of business in the field.
Many progressive products have been brought to the company. Its clients range from an individual designer to a product design division of top-notch corporations.
Rapiro & Bocco
One of the major products handled by the company is the development of “Rapiro”, a humanoid robot kit for education, a collaborative production with Kiluck and Switch Science. It’s a programmable DIY robot kit, which comes with 12 servomotors and an Arduino compatible Rapiro main board, designed for Raspberry Pi. The company produced the mold for the parts and manufactures the product in their factory. It made a big hit in Kickstarter campaign in 2013, and it is still selling well worldwide.
Another well-known product could be “Bocco”, a family communication robot, designed and produced by Yukai Engineering. It received Good Design Award 2015 and the 10th Kids Design Award in 2016.
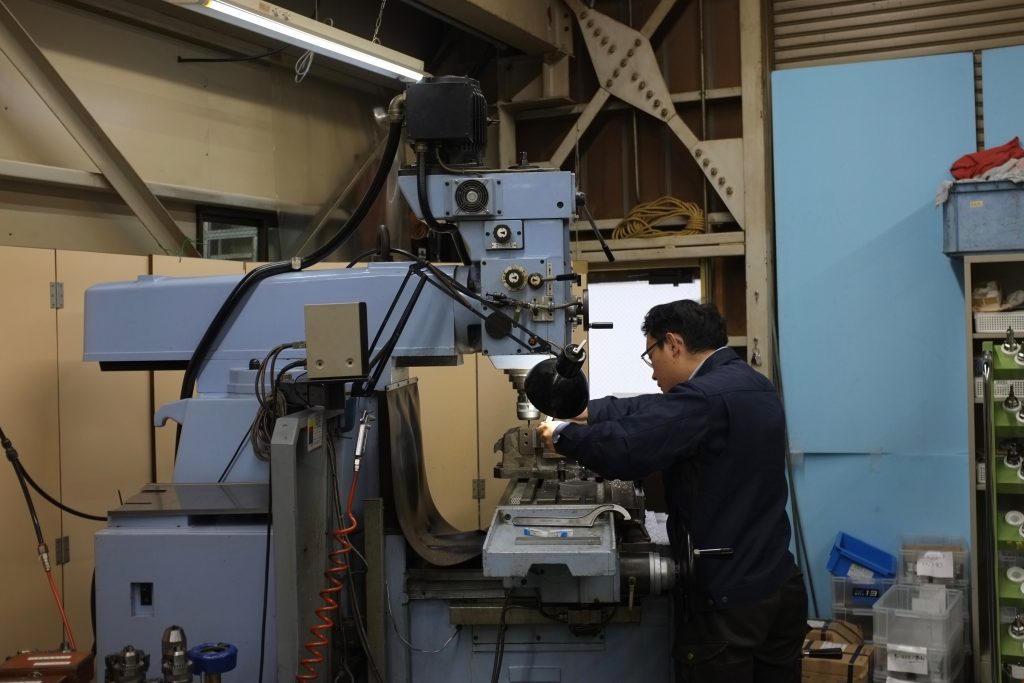
A simple mold for prototyping and small volume production
These clients rely on Miyoshi with its supreme quality, affordable price, and good service. Not that they have no other factories to choose from, in fact, some do know many factories in China and Taiwan, but still, they choose the company.
The price competitiveness comes from their skill and knowledge in using aluminum for simple molds. As aluminum is easier to process than steel or other metals, it would reduce the material and the labor cost, and shortens the delivery period. Durability is relatively low, but it fits well for small volume production and prototyping.
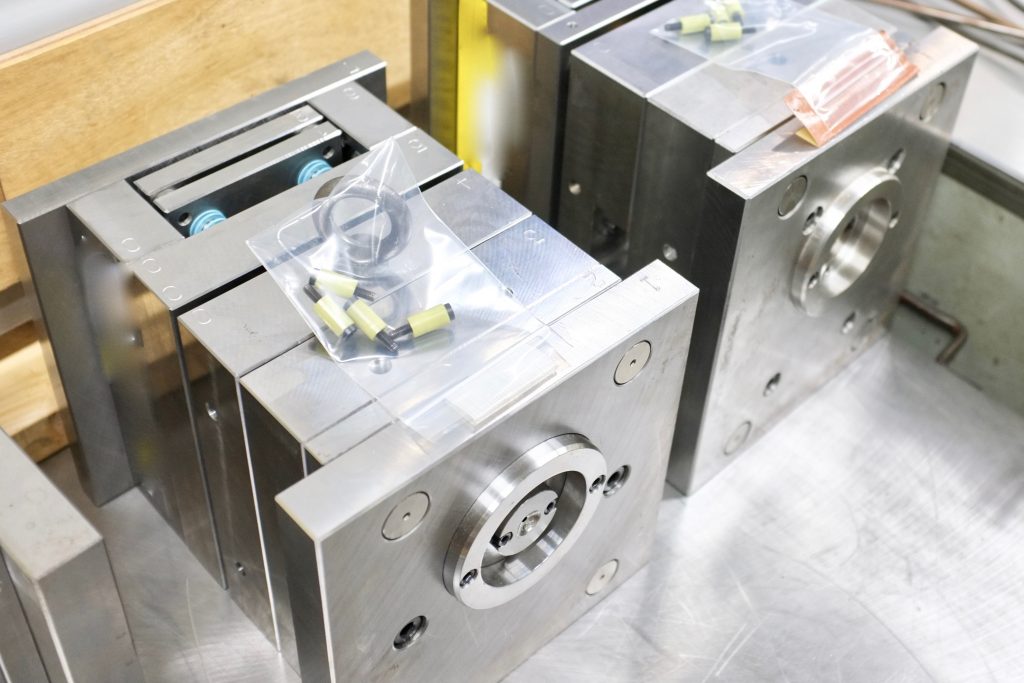
Environmentalist producing plastic products
Working with products such as Rapiro and Bocco is ideal for Sugiyama. The users love these products and the quality is good to last long. He puts great efforts to produce products that matter to people and be used for years.
He even made an original measuring tool for designers and engineers shaped in a chocolate bar so that it could fit as an interior on the desk. The package was also designed as a container of the product, not to be wasted.
His efforts as an environmentalist don’t stop here. In January 2017, the company won the Energy Conservation Grand Prize from the Energy Conservation Center, Japan, sponsored by Ministry of Economic, Technology, and Industry (METI). An honor was given to the company for its outstanding performance to reduce the energy consumption of the factory by 33.7 percent in 2015 from its level in 2007.
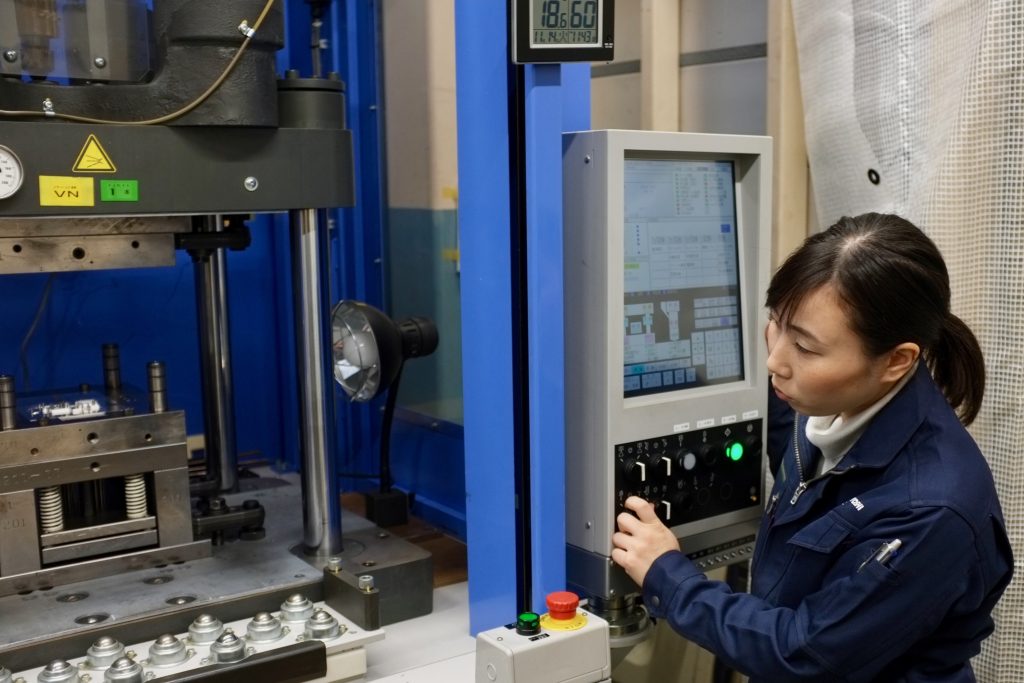
The Team Miyoshi
The Award especially took note of the contribution of the employees, who worked closely together as a team. Currently, there are 19 employees including 7 part-time staffs working in the factory, many are women. Sugiyama says it’s important that the employees share his value.
“We have 5 axis machining center and various state-of-art machinery and equipment. But what really matters is the experience we have in understanding the client’s needs, precaution we take in design and production process, and high skill of finishing the goods such as hand polishing.”
He plans to increase his team to more than 20 full-time employees. However, he said, “It’s not easy”. He explained that none of his employees has engineer background before working with the company. “Young Japanese engineers tend to avoid choosing a small factory like us for a career. They prefer large corporations for stable income and career development.”
But that doesn’t discourage him. He is now occasionally holding a workshop where young people can experience manufacturing at his factory. He is actively working on promoting local small and medium factories and manufacturing.
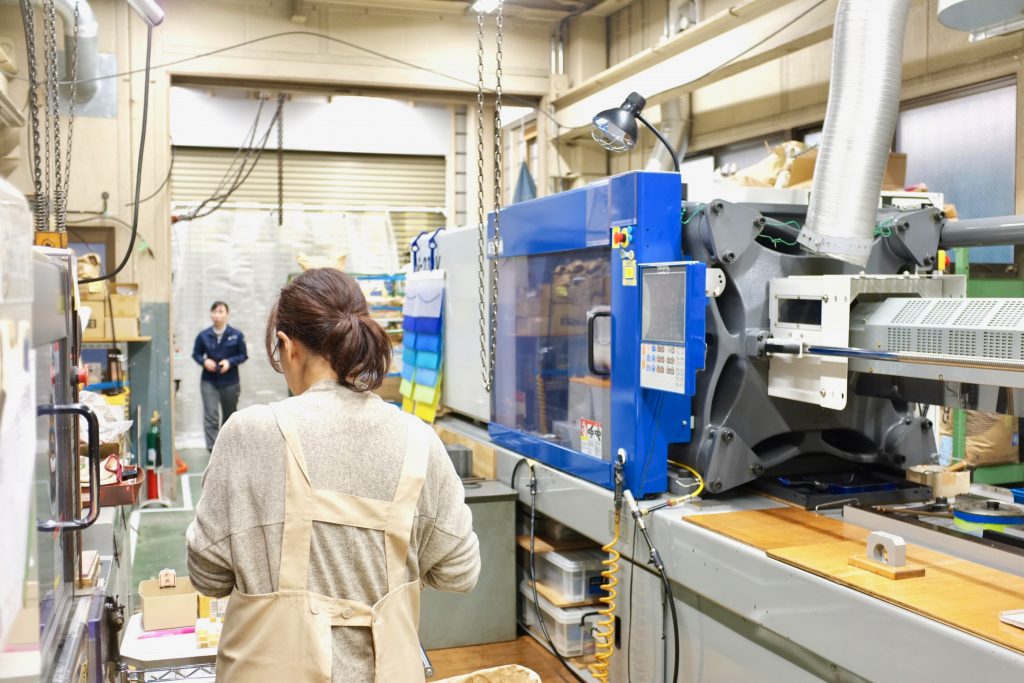
A man with a vision
Sugiyama is a unique person. He’s a kind of person you find in an old Japanese samurai movie: quiet, calm, but dead straight in business. He chooses his words and he means it when it comes out.
But he is also a product of his generation: young, active, bright, and open to new opportunities. He knows that the changes are must: a challenge is not to avoid but to embrace. Setting his eyes ahead, he puts his feet on the ground. He is one of the most active factory owners in Katsushika: eager to learn new things and expand his network.
I asked him about the company’s future plan. “I want to transform my company to become a manufacturer of factory machines and equipment for production of eco-friendly products. We are still small and there’re so much to accomplish ahead. But we believe in our future and, eventually, we’ll reach there.” said Sugiyama. Well, I say no doubt about it.